Análisis Profundo: Cómo Eliminar Vibraciones en Equipos Industriales y Extender su Vida Útil
Introducción: Las vibraciones no son solo ruido
Las vibraciones en sistemas mecánicos son mucho más que una simple molestia acústica. Representan señales de alerta temprana que, si se ignoran, pueden desencadenar fallos catastróficos. Por ejemplo, un desbalance mínimo de 50 micras en el rotor de un ventilador industrial puede reducir la vida útil de los rodamientos entre un 30% y 40%. En entornos de alta exigencia, como la industria pesada o la generación de energía, las vibraciones no controladas provocan desde fisuras en soldaduras hasta el colapso prematuro de cimentaciones.
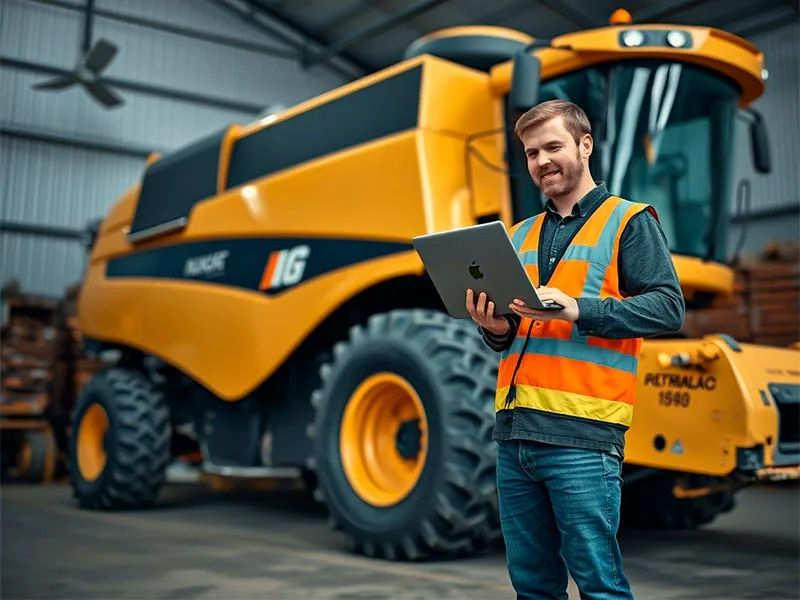
La pregunta crítica es: ¿cómo distinguir entre vibraciones operacionales «normales» y aquellas que anuncian un fallo inminente? Este artículo no solo responderá esa pregunta, sino que proporcionará metodologías probadas en campo para diagnosticar y corregir estos problemas de raíz.
Diagnóstico: De los síntomas a la causa raíz
1.1. Fuentes principales de vibraciones
Desbalance del rotor (60% de los casos): Causado por distribución desigual de masa, acumulación de contaminantes o desgaste asimétrico.
Desalineación de ejes: Una desviación de apenas 0.1 mm por metro de longitud puede triplicar la amplitud vibratoria.
Fallas en rodamientos: Identificables mediante patrones de armónicos específicos en análisis espectral.
Resonancia estructural: Ocurre cuando la frecuencia operacional coincide con la frecuencia natural del equipo o su base.
1.2. Técnicas de análisis avanzado
Vibrometría (ISO 10816): Útil para mediciones básicas, pero insuficiente para diagnóstico profundo.
Análisis espectral (FFT): Revela frecuencias dominantes asociadas a desbalance, desalineación o fallas en engranajes.
Marcado de fase: Técnica indispensable para balanceo dinámico in situ.
Análisis modal: Identifica modos de vibración resonantes en estructuras complejas.
Caso real: En un molino de cemento, un reductor exhibía vibraciones de 12 mm/s (frente a un límite seguro de 4.5 mm/s). El análisis FFT detectó un pico en 2× la frecuencia de rotación, indicando desalineación angular. Tras la corrección con láser, los niveles cayeron a 3.2 mm/s.
Soluciones Duraderas (más allá de los parches temporales)
2.1. Balanceo de precisión
Balanceo estático: Aplicable a rotores cortos (ej. discos de corte).
Balanceo dinámico: Obligatorio para turbinas, ventiladores y rotores largos. Equipos como el Scheffield Balancer permiten correcciones sin desmontaje.
Error frecuente: Intentar balancear un rotor con rodamientos dañados. Siempre debe verificarse primero el estado de los componentes.
2.2. Alineación láser de ejes
Precisión de 0.01 mm: Tecnologías como Easy-Laser superan 10 veces los métodos mecánicos.
Alineación en caliente: Esencial para turbinas o bombas que operan con gradientes térmicos significativos.
2.3. Control activo y pasivo de vibraciones
Amortiguadores piezoeléctricos: Usados en turbinas de alta precisión para supresión en tiempo real.
Aisladores elastoméricos: Seleccionados según rigidez y rango de frecuencias críticas.
Casos no convencionales: Cuando las reglas fallan
3.1. Resonancia encubierta
Problema: Una bomba centrífuga vibraba excesivamente a 1500 RPM, pese a estar balanceada.
Solución: El análisis modal reveló resonancia estructural a 1490 RPM. Se modificó la rigidez de la base, desplazando la frecuencia crítica fuera del rango operacional.
3.2. Causas no mecánicas
Vibraciones electromagnéticas: En motores, si desaparecen al cortar la alimentación, indican problemas en el estator o entrehierro.
Pulsaciones hidráulicas: Causadas por cavitación o diseño inadecuado de impulsores en bombas.
Análisis espectral periódico: Detecta patrones de desgaste incipiente (ej. fisuras en engranajes).
Capacitación técnica: El 80% de los problemas graves se previenen con alineación y montaje inicial correctos.
Regla de oro: Nunca suprimir vibraciones con amortiguadores sin antes eliminar su causa. Un equipo bien ajustado es silencioso por naturaleza.